Mantenimiento productivo total (TPM): ¿Qué es y para que sirve?
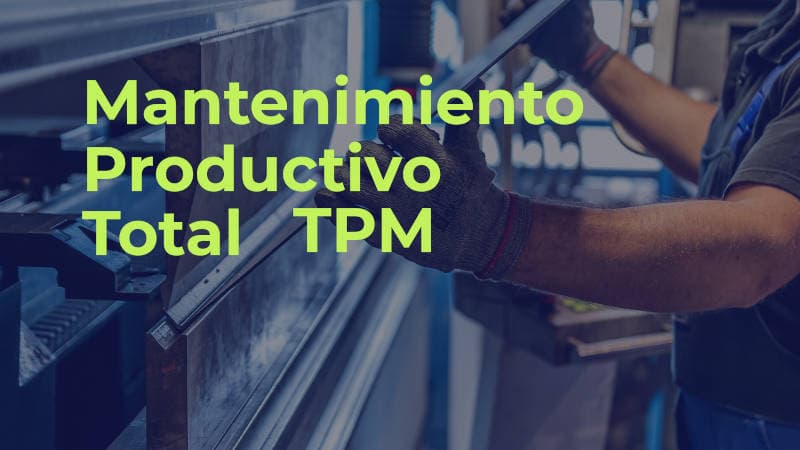
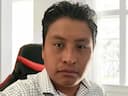
by Juan Carlos García
25-Febr-2024
(3)
Post relacionados
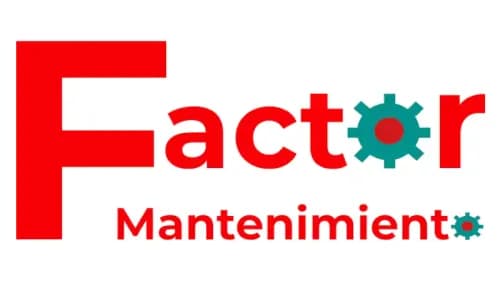
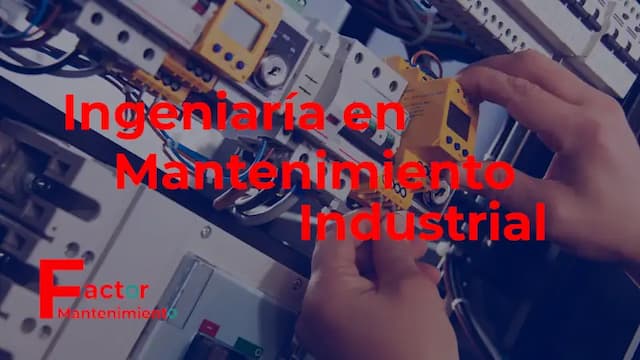
Ingeniería en mantenimiento industrial
Ingeniería en mantenimiento industrial: clave para la eficiencia y productividad
(2)
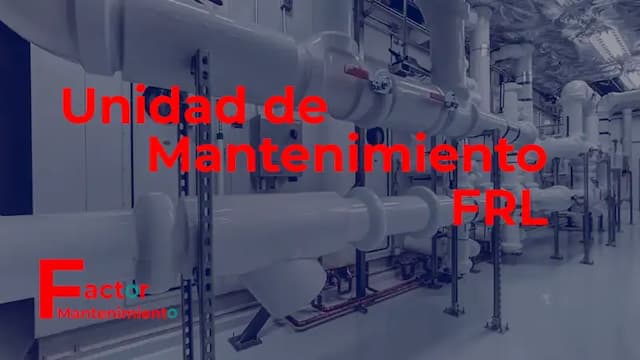
Unidad de mantenimiento
Todo lo que debes saber sobre la unidad de mantenimiento en sistemas neumáticos
(2)
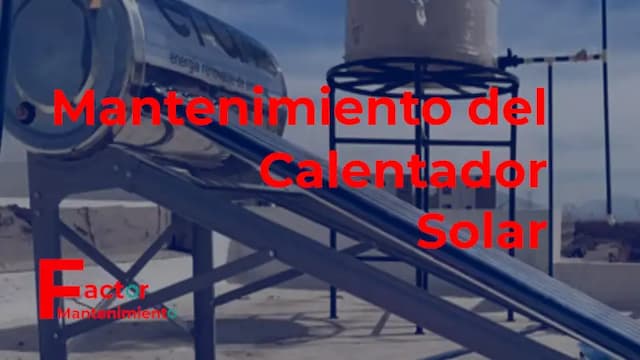
Mantenimiento calentador solar
Mantenimiento calentador solar: Guía completa de mantenimiento y cuidados para nuestros calentadores solares
(4)
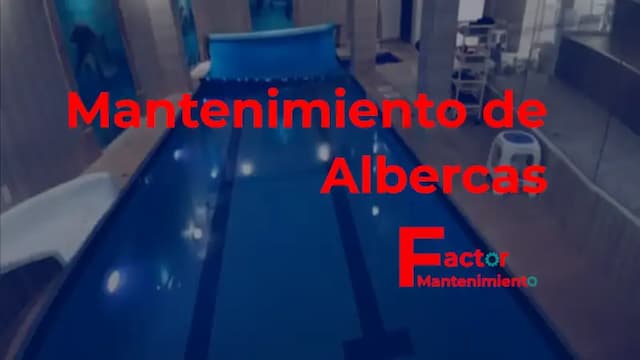
Mantenimiento de albarcas
Guía de mantenimiento de albercas: Consejos y recomendaciones esenciales
(1)
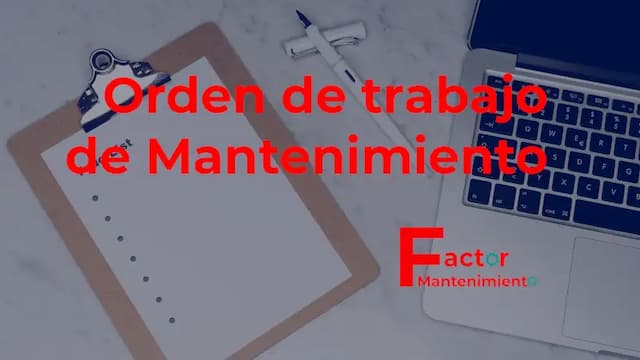
Orden de trabajo de mantenimiento
Orden de trabajo de mantenimiento: Creación, planificación para gestionar tareas eficientemente
(1)

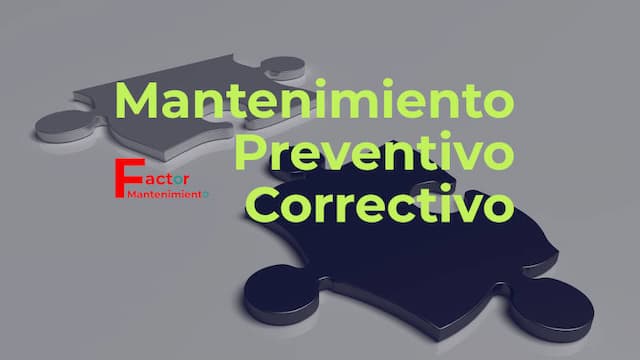
Mantenimiento preventivo y correctivo
Mantenimiento preventivo y correctivo: ¿Qué son? Y ¿Qué los diferencia?
(1)
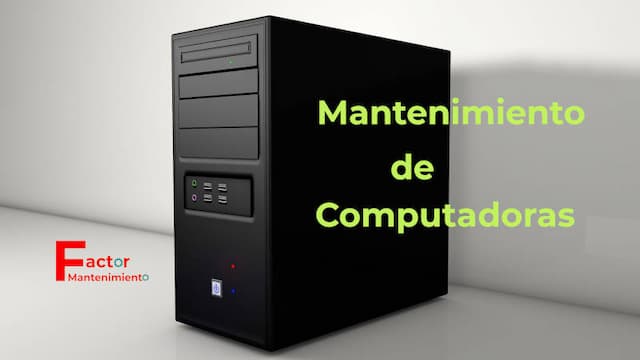
Mantenimiento de computadoras
Mantenimiento preventivo de computadoras: Plan en Excel, herramientas y mucho más.
(3)
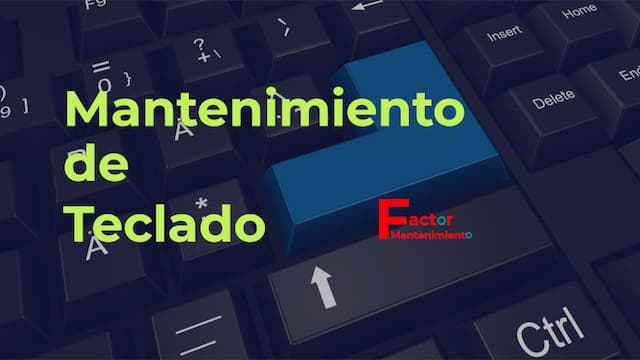
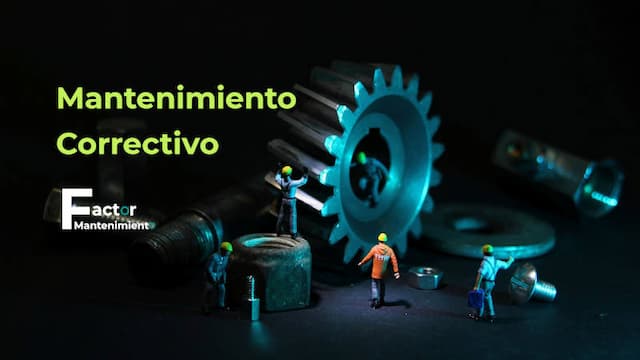
Mantenimiento correctivo
Mantenimiento correctivo: ¿Qué es? Tipos, ventajas y desventajas.
(2)
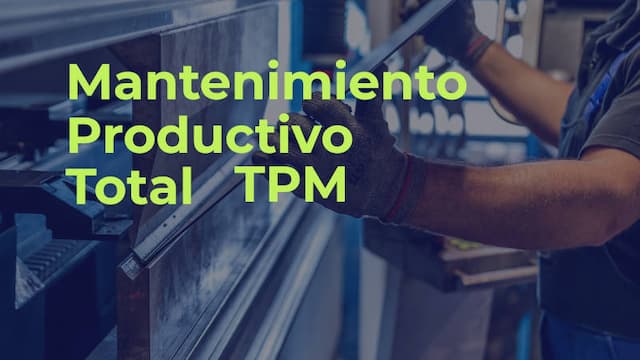
Mantenimiento productivo total
Mantenimiento productivo total (TPM): ¿Qué es y para que sirve?
(3)
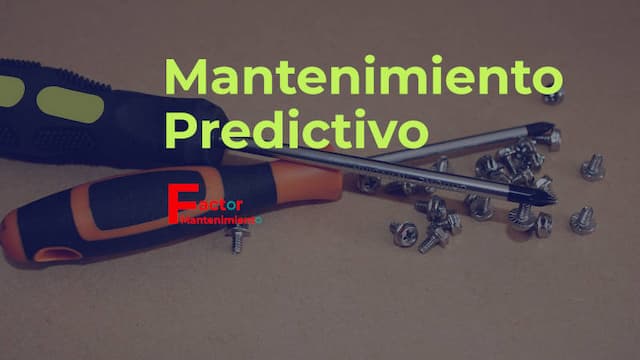
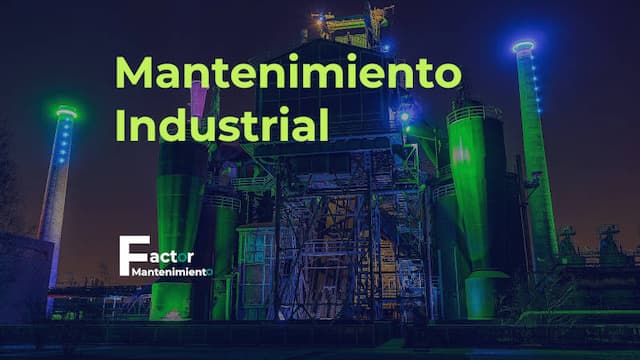
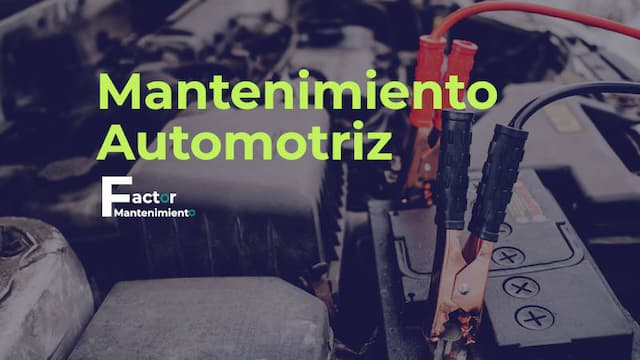
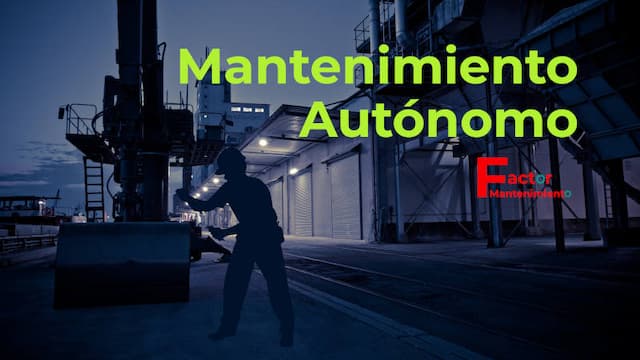
Mantenimiento Autónomo
Los 8 pasos esenciales del Mantenimiento Autónomo y el principio japonés de las cinco "S"
(1)
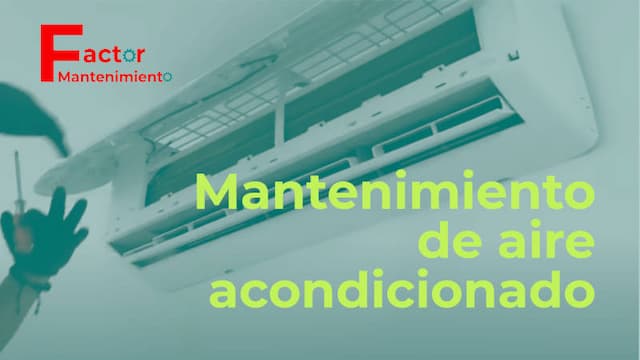
Mantenimiento de aire acondicionado
¿Cómo hacer un correcto mantenimiento del aire acondicionado?
(1)
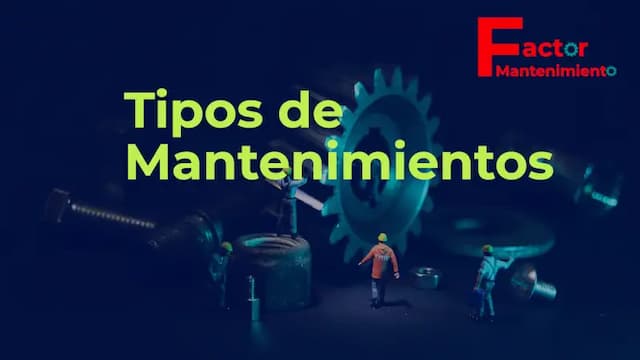
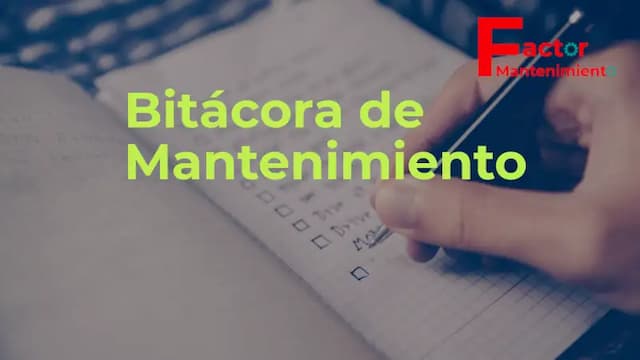
Bitácora de mantenimiento
Bitácora de mantenimiento: Todo lo que necesitas saber para crear tus propias bitácoras de mantenimiento
(2)
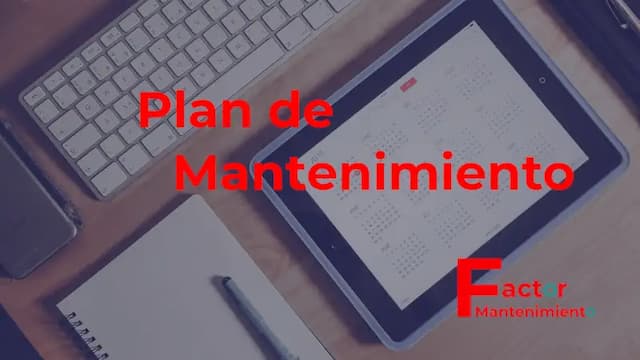
Plan de mantenimiento
Plan de mantenimiento: cómo implementarlo en tu empresa para garantizar la continuidad del negocio.
(2)
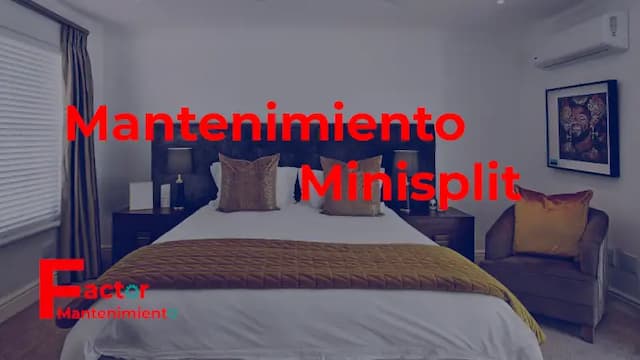
Mantenimiento de minisplit
Guía completa de mantenimiento de minisplit: cómo mantener tu equipo en óptimas condiciones
(1)
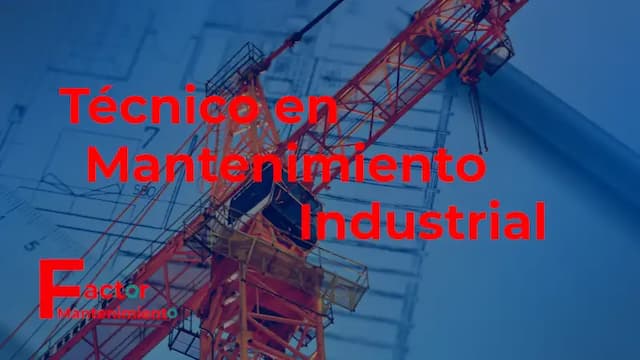
Técnico en Mantenimiento
Técnico en Mantenimiento: Perfil, Funciones y Oportunidades Laborales
(1)
Hola, bienvenidos, el día de hoy analizaremos cómo surgió el concepto de mantenimiento de producción total (TPM), sus objetivos, características principales que lo distinguen, así como los procesos que pueden estar involucrados.
Conocerás las ventajas y desventajas que puede traer su incorporación en una compañía. Y también conocerás cómo aplicar este tipo de mantenimiento de manera efectiva.
Una de las cosas que las empresas en todos los niveles y emprendedores toman muy en cuenta es la reducción de costos y el aumento en las ganancias.
A medida en que crecen dentro del mercado y a pesar del aumento en sus ventas traducidas en ganancias, deben sopesar mayores gastos e inversiones conforme crecen.
Tabla de contenido
- 1 ¿Qué es el mantenimiento productivo total?
- 2 Historia del mantenimiento productivo total
- 3 Objetivos del mantenimiento productivo total
- 4 Características principales
-
5 ¿Cómo aplicar el mantenimiento productivo total?
- 5.1 1 Planificación
- 5.2 2 Formación del equipo de implementación
- 5.3 3 Sensibilización y compromiso de la alta dirección
- 5.4 4 Identificación de los equipos críticos y establecimiento de equipos de trabajo
- 5.5 5 Análisis de la situación actual
- 5.6 6 Desarrollo del plan de mejora
- 5.7 7 Implementación del plan de mejora
- 5.8 8 Formación y capacitación del personal
- 5.9 9 Medición y seguimiento de los resultados
- 6 10 Mejora continua
- 6 Ventajas del mantenimiento productivo total
- 7 Desventajas del mantenimiento productivo total
-
8 Los 8 pilares del mantenimiento productivo total
- 8.1 1. Kobetsu Kaizen o mejoras enfocadas:
- 8.2 2. Jushu Hozen o Mantenimiento Autónomo:
- 8.3 3. Mantenimiento especializado:
- 8.4 4. Mantenimiento planificado o progresivo:
- 8.5 5. Hinshitsu Hozen o Mantenimiento de calidad:
- 8.6 6. Mantenimiento en la administración:
- 8.7 7. Capacitación y entrenamiento constante:
- 8.8 8. Seguridad y ambiente favorable:
- 9 Empresas que han implementado el TPM con éxito
- 10 Herramientas y técnicas de TPM
- 11 3 ejemplos de mantenimiento productivo total
- 12 Dificultades y desafíos del TPM
- 13 Futuro del TPM
- 14 Resumen
Dentro de los gastos empresariales más costosos tenemos la reparación y mantenimiento especializado que deben darle a la maquinaria y equipos que necesitan para operar.
Al tratarse de procedimientos no contemplados dentro de las actividades de la organización, es necesario la inminente contratación de personal externo con conocimientos especializados y sin mencionar los costos en refacciones o en su caso, la compra de nuevo equipo.
El costo más grande lo encontramos en la pérdida de tiempo en el que la maquinaria es reparada y hasta que pueda volver a operar, esto reduce su producción en gran medida.
Antes las compañías necesitan mantener una organización e implementar varios procesos aislados que resolvieran problemas de producción y también buscarán la mejora de una parte específica de la producción.
Actualmente establecen un sistema automatizado para gestionar todos sus niveles de producción y administración, pero este por sí mismo no puede acaparar todas las actividades de la empresa, a menos que se coordine como un todo.
Para obtener el mayor provecho del sistema automatizado requiere de la coordinación de todos los sectores: producción, organización y humano.
En caso de que uno falle o se retrase se presentaría una gran posibilidad de colapso o retraso, una gran pérdida económica.
Ahora, la producción de cualquier tipo de bien o servicio requiere del avance tecnológico y sistemas automatizados, pero también se necesita un buen plan de producción y de prevención de imprevistos.
Para evitar problemas y aumentar resultados dentro de nuestra empresa es importante hablar del mantenimiento productivo total, cuya cualidad principal es la inclusión del recurso humano en el sostenimiento y mayor provecho de los equipos.
Se establece correctamente permitirá que se cumplan con controles de calidad y satisfacción de los clientes, así como tener un control de todas las operaciones.
¿Qué es el mantenimiento productivo total?
El mantenimiento productivo total o “Total Productive Maintenance” (TPM) es una práctica de gestión del mantenimiento de equipos, procesos de producción, organización del personal, etc., para mantener su eficiencia e incluso, aumentar sus operaciones y obtener mayor provecho de los equipos.
Es una herramienta de eficiencia y competitividad para empresas, sobre todo si tienen operaciones automatizadas, ya que permite a los sistemas automatizados cumplir con especificaciones de calidad, tiempo y costo de producción.
El TPM Consiste en combinar una serie de actividades y técnicas para un aprovechamiento mejorado de la capacidad de producción que requiere de varios procesos que lo convierten en un sistema muy eficiente para controlar toda la maquinaria industrial, es decir, todos sus recursos e incluso el humano.
El TPM tienen una estrecha relación con el mantenimiento preventivo que le dio vida.
Tomando en cuenta que, el mantenimiento preventivo consiste en brindar un conjunto de técnicas para prever errores, daños por el simple paso del tiempo o contratiempos en algún equipos o procesos para mantenerlos funcionales y ampliar su vida útil, mediante una revisión constante y periódica.
Encontramos que la relación del mantenimiento productivo total y el mantenimiento preventivo está en la evolución del mejoramiento de los equipos para evitar que fallen y aprovechar conocimientos operativos para aumentar la vida útil, con las llamadas “mejoras incrementales”.
Esta relación se hace más notoria al llegar la automatización, ya que se requiere un mantenimiento más sostenible donde todos los recursos tanto materiales, económicos y humanos colaboran en procesos preservación como el mantenimiento de las maquinarias, llegando a reducir costos y minimizando la inactividad.
Historia del mantenimiento productivo total
Según Gómez, al introducirse en Japón el concepto de mantenimiento preventivo en los cincuenta y la creación del concepto Kaizen (mejora continua) en los setentas, se visualizó al mantenimiento como una manera de mejorar la fiabilidad de los equipos.
Debe ser de forma permanente a través de la inclusión de los trabajadores en este aspecto tan importante.
Encontrando que el concepto de mantenimiento productivo total (TPM) fue creado por Nippon Denso del grupo Toyota en 1960.
La estrategia del señor Denso fue capacitar a todos sus operarios de maquinaria de forma que fueran capaces de conocer y realizar el mantenimiento del equipo que manejaban.
Gracias a sus esfuerzos, la compañía obtuvo resultados considerables a partir de 1969.
Es aquí donde se crea el mantenimiento productivo. Actualmente, el TPM que busca el trabajo conjunto de todos los elementos de una empresa para conservar y dar mantenimiento a los equipos de producción.
Se considera una estrategia agresiva enfocada en obtener la mayor eficiencia del equipo con el que se cuenta e integrar al personal de la industria en todos los niveles de producción.
Es posible que se considere agresiva por ser un cambio muy importante y extendido, ya que consta de la inserción de varios procesos según las necesidades.
Con el tiempo, el mantenimiento productivo total fue evolucionando y mejorando hasta llegar a ser implementado en varios negocios.
Debido a su enfoque de no solo mantener los equipos funcionando, sino que, mejora la productividad de forma total. Su secreto está en hacer uso correcto de todos los recursos disponibles del conglomerado.
Objetivos del mantenimiento productivo total
Los objetivos característicos del mantenimiento productivo total son:
- Mejorar la calidad en los productos al evitar defectos de fabricación, choque de procesos o retrasos en entregas.
- Reducción de costos al tener organización y explotación de todos los recursos disponibles.
- Acortar plazos al tener fiabilidad del funcionamiento de las etapas de producción.
- Búsqueda de una mayor eficiencia involucrando al hombre, los equipos y los sistemas de la empresa[7]en conjunto.
Características principales
Lo que caracteriza al mantenimiento productivo total es:
- Mantenimiento continuo al equipo.
- Amplia participación del recurso humano y su capacitación.
- Es una estrategia global.
- Busca efectividad de las operaciones en todos los aspectos de la producción y de la empresa. No solo mantiene en buen estado el material de trabajo.
- Cuidado y preservación de los equipos por todo el personal. No solo de los técnicos especializados.
- Establecimiento de procesos de mantenimiento relacionados al conocimiento que el personal tiene del equipo y sus procesos.
- Capacitación y entrenamiento del personal.
La diferencia que tiene con el mantenimiento productivo es la integración del recurso humano al mantenimiento y mejora de los equipos, no solo del equipo en sí mismo.
¿Cómo aplicar el mantenimiento productivo total?
En este punto, podemos darnos cuenta de que el mantenimiento va mucho más allá de acciones aisladas que se realizan para crear eficiencia, sino que es un sistema programado que requiere ser coordinado y establecido acorde con el tipo de negocio o el tamaño de la empresa para que genere resultados.
Por tanto, el mantenimiento productivo total debe ser estratégicamente planificado y estructurado al momento en que se encuentra la empresa.
Aquí te presento un paso a paso para implementar el TPM (Mantenimiento Productivo Total) en una empresa:
1 Planificación
- Se debe establecer un plan de acción para la implementación del TPM.
- Esto implica la definición de objetivos y metas claras, identificación de los equipos críticos y áreas de mejora, asignación de roles y responsabilidades del equipo de implementación, y establecimiento de un cronograma de implementación.
2 Formación del equipo de implementación
- Seleccionar a un equipo interdisciplinario que se encargará de liderar la implementación del TPM en la empresa.
- Es importante que los miembros del equipo tengan habilidades técnicas, de comunicación y liderazgo para poder llevar a cabo el proceso de implementación.
3 Sensibilización y compromiso de la alta dirección
- Es importante que la alta dirección esté comprometida con el proceso de implementación del TPM, ya que esto dará el apoyo necesario para llevar a cabo la implementación.
- La alta dirección debe comunicar la importancia del TPM a todos los empleados y asegurarse de que entiendan su importancia.
4 Identificación de los equipos críticos y establecimiento de equipos de trabajo
- Es necesario identificar los equipos críticos que se someterán al proceso de mejora continua.
- Posteriormente, se debe establecer un equipo de trabajo para cada equipo crítico, el cual estará conformado por personal de diferentes áreas de la empresa.
5 Análisis de la situación actual
- Se debe realizar una evaluación de la situación actual del equipo crítico, identificando los problemas y oportunidades de mejora.
- Se pueden utilizar herramientas como el diagrama de Pareto, el análisis de causa-efecto o el análisis FMEA para identificar los problemas y las causas raíz.
6 Desarrollo del plan de mejora
- Se debe establecer un plan de mejora para cada equipo crítico, identificando las acciones específicas que se tomarán para abordar los problemas identificados en el paso anterior.
- El plan debe establecer objetivos, metas y plazos claros para la implementación.
7 Implementación del plan de mejora
- Se deben llevar a cabo las acciones específicas identificadas en el plan de mejora.
- Es importante que se cuente con el apoyo de toda la organización para llevar a cabo las mejoras.
8 Formación y capacitación del personal
- Es importante capacitar al personal de la empresa en las técnicas y herramientas del TPM.
- Esto ayudará a crear una cultura de mejora continua en la organización.
9 Medición y seguimiento de los resultados
- Se deben establecer indicadores de desempeño para medir los resultados de la implementación del TPM.
- Estos indicadores deben ser medidos de forma periódica y comparados con los resultados anteriores a la implementación del TPM.
- De esta manera, se podrá evaluar el éxito de la implementación y hacer ajustes en caso de ser necesario.
10 Mejora continua
- El TPM es un proceso de mejora continua, por lo que se debe seguir trabajando en la mejora de los equipos y procesos en la empresa.
- Se deben identificar nuevas áreas de mejora y establecer nuevos planes de mejora para seguir mejorando la eficiencia y eficacia de los equipos y procesos.
Ventajas del mantenimiento productivo total
Dentro de las ventajas de establecer un mantenimiento productivo total bien implementado encontramos:
- En la organización: mejorará la calidad en el ambiente de trabajo, mayor control de operaciones y fomento de una cultura de responsabilidad, respeto y disciplina.También tenemos capacitación constante, participación total de todas las personas, conocimiento del número de empleados requeridos y mayor comunicación.
- En la seguridad: mayor seguimiento de las reglas de seguridad, prevención de riesgos tanto del equipo como el cuidado en la salud de los empleados, mayor capacidad en la identificación de problemas e implementó inmediato de acciones correctivas, así como la reducción de accidentes y fuentes de contaminación.
- En la productividad: evitar pérdidas en la producción, mejorar la fiabilidad y disponibilidad de equipos, reducción de costos por mantenimiento, mayor calidad en productos finales, evitar recambios por defectos y estar preparados para la implementación tecnológica. También permitirá adaptarse a los cambios del mercado rápidamente aumentando la competitividad.
Desventajas del mantenimiento productivo total
- Las desventajas consisten en la mala planificación y no considerar imprevistos.
- Es una mala planificación si no toma en cuenta los fines y objetivos de la empresa, si no se implementa de manera escalonada según el momento en el que se encuentre la empresa o si se capacita al personal antes de darle mayores responsabilidades.
- En tanto, la no consideración de imprevistos es muy importante para evitar retrasos o colapsos de los sectores, para esto se debe tener en cuenta una cultura de prevención y supervisión constante.
Los 8 pilares del mantenimiento productivo total
Gómez señala los siguientes procesos fundamentales para el mantenimiento productivo total:
1. Kobetsu Kaizen o mejoras enfocadas:
- Requiere la intervención de diferentes áreas del proceso productivo y pretende maximizar la efectividad general de equipo, procesos y sectores.
- Es un trabajo organizado en equipos funcionales e interfuncionales con métodos específicos.
- Centra su atención en eliminar pérdidas existentes.
2. Jushu Hozen o Mantenimiento Autónomo:
- El TPM requiere de la implementación del mantenimiento autónomo y el de mayor impacto, pues consiste en involucrar al recurso humano y aplicar el conocimiento que tiene un operador para dominar el equipo, conocer sus fallas, cuidados, manejo y conservación.
- Es indispensable en el TPM porque ayudaría a la detección de problemas, requerimiento de mantenimiento y prever averías en la maquinaria e incluso el mismo personal podría brindar mantenimiento preventivo.
- Se obtiene aplicando capacitaciones constantes al personal.
3. Mantenimiento especializado:
En este existen tres opciones:
- La primera es tomar un grupo de trabajadores elegidos por su eficiencia e invertir en su especialización que les permita, en un futuro, realizar reparaciones o resolver problemas que un trabajador normal no podría.
- La segunda opción es contratar personas especialistas de planta.
- La tercera y más costosa es tener un acuerdo con una empresa especializada que brinde de manera pronta atenciones especializadas a los equipos.
4. Mantenimiento planificado o progresivo:
- Elimina los problemas en la maquinaria con acciones de mejora, prevención y predicción.
- Para dar un mejor mantenimiento se crea una base de datos que se nutre a partir de cada revisión.
5. Hinshitsu Hozen o Mantenimiento de calidad:
- Mejora la calidad de los productos finales y aumenta la viabilidad por medio de control de componentes y condiciones que impactan en las características de calidad del producto.
- Es un tipo de mantenimiento preventivo enfocado al cuidado del producto.
6. Mantenimiento en la administración:
- No se produce un valor directo, pero coordinan, facilitan y ofrecen apoyo durante todo el proceso productivo, verifica que se realice la producción a menores costes y con alta calidad.
- Solo ofrece información.
7. Capacitación y entrenamiento constante:
- Se centra en el desarrollo de habilidades en el personal.
- El fin es que los trabajadores puedan identificar y detectar problemas en los equipos, conocer el funcionamiento, establecer la relación entre el equipo y la calidad, logren resolver problemas de operación y durante los procesos, trabajar en conjunto y enseñar a otros.
8. Seguridad y ambiente favorable:
- Capacitación y conocimiento del porque las medidas de seguridad. Tomar en consideración el ambiente laboral y mejorarlo para que sea más productivo y evite problemas.
Estos procesos trabajan en conjunto y es posible que no siempre estén implementados, esto ya dependerá de las características, principios, misión, visión, fines y desarrollo del negocio que se trate. Incluso depende del producto final que se desarrolle (bien o servicio).
Empresas que han implementado el TPM con éxito
A continuación, se presentan algunos casos de empresas que han implementado con éxito el TPM y han visto mejoras significativas en su productividad y eficiencia:
- Toyota: Toyota es uno de los primeros usuarios del TPM. En la década de 1960, la compañía comenzó a implementar el TPM en sus plantas de producción. A través del TPM, Toyota pudo mejorar la eficiencia de sus máquinas y equipos, reducir los costos de producción y mejorar la calidad de sus productos. Actualmente, el TPM es parte integral de la cultura de Toyota y se ha extendido a sus proveedores y distribuidores.
- Nissan: Nissan implementó el TPM en sus plantas de producción en Japón en la década de 1980. A través del TPM, la compañía logró mejorar la eficiencia de sus máquinas y equipos, reducir los costos de producción y mejorar la calidad de sus productos. Nissan también implementó el TPM en sus plantas de producción en todo el mundo y ha visto mejoras significativas en su productividad y eficiencia.
- Bridgestone: Bridgestone, el fabricante japonés de neumáticos, implementó el TPM en sus plantas de producción en la década de 1990. A través del TPM, Bridgestone logró reducir el tiempo de inactividad de las máquinas, mejorar la eficiencia de la producción y mejorar la calidad de sus productos. La compañía también implementó el TPM en sus plantas de producción en todo el mundo y ha visto mejoras significativas en su productividad y eficiencia.
- Unilever: Unilever, el fabricante británico de productos de consumo, implementó el TPM en sus plantas de producción en la década de 1990. A través del TPM, Unilever logró mejorar la eficiencia de sus máquinas y equipos, reducir los costos de producción y mejorar la calidad de sus productos. La compañía también implementó el TPM en sus plantas de producción en todo el mundo y ha visto mejoras significativas en su productividad y eficiencia.
El TPM es una metodología efectiva para mejorar la eficiencia de la producción y la calidad de los productos. Las empresas mencionadas anteriormente han implementado con éxito el TPM y han visto mejoras significativas en su productividad y eficiencia.
Herramientas y técnicas de TPM
El TPM o Mantenimiento Productivo Total es una metodología que tiene como objetivo aumentar la eficiencia de los equipos de producción a través de la reducción de pérdidas en todos los aspectos, desde la maquinaria hasta el personal.
A continuación, se presentan algunas herramientas y técnicas utilizadas en el TPM:
Análisis de pérdidas
- Consiste en identificar y medir las pérdidas que se producen en la producción y proponer soluciones para eliminarlas.
- Las pérdidas pueden ser de diferentes tipos, como pérdidas de velocidad, pérdidas de calidad y pérdidas de disponibilidad.
Mejora del mantenimiento
- En esta técnica se busca mejorar la eficacia del mantenimiento preventivo y correctivo.
- Para ello se pueden utilizar herramientas como el análisis FMEA (Análisis de Modo y Efecto de Fallas) para identificar posibles fallos, y el análisis de causa raíz para determinar las causas subyacentes de los problemas.
Mantenimiento autónomo
- Esta técnica implica que el personal de producción se encargue de realizar tareas de mantenimiento simples y de limpieza en las máquinas.
- Esto ayuda a reducir el tiempo de inactividad de la máquina y a mejorar la calidad del producto.
Formación y capacitación
- Es importante que el personal de producción reciba la formación y capacitación necesaria para poder implementar las técnicas de TPM de manera efectiva.
- Esto puede incluir la formación en técnicas de solución de problemas, herramientas de mejora continua y técnicas de mantenimiento.
Mejora de la calidad
- La mejora de la calidad es fundamental en el TPM ya que ayuda a reducir las pérdidas asociadas con la producción de productos defectuosos.
- Las herramientas de mejora de calidad pueden incluir el control estadístico de procesos, el análisis de Pareto y el diagrama de Ishikawa.
Gestión visual
- Se trata de una técnica que utiliza gráficos y tableros visuales para ayudar a identificar problemas y oportunidades de mejora en la producción.
- Esto puede incluir la utilización de gráficos de control para identificar tendencias y anomalías en la producción y tableros de indicadores clave de rendimiento (KPI) para medir la eficacia de las técnicas de TPM.
Estas son solo algunas de las herramientas y técnicas utilizadas en el TPM. La elección de las técnicas adecuadas dependerá del tipo de proceso productivo, la maquinaria involucrada y las necesidades específicas de la empresa.
3 ejemplos de mantenimiento productivo total
Aquí te presento 3 ejemplos de mantenimiento productivo total:
1 Cambio rápido de herramientas (SMED)
- Esta herramienta de TPM se enfoca en reducir el tiempo que se tarda en cambiar las herramientas de una máquina para que pueda comenzar a producir otro producto.
- Este proceso es importante para lograr la flexibilidad en la producción y una mayor eficiencia.
2 Mantenimiento autónomo
- Este tipo de mantenimiento implica que los operadores de las máquinas sean responsables del mantenimiento diario y la limpieza de las mismas.
- Los operadores reciben capacitación para realizar pequeñas reparaciones, lo que reduce la necesidad de intervención del personal de mantenimiento y mejora el tiempo de disponibilidad de la máquina.
3 Análisis de modos y efectos de fallas (AMEF)
- Esta técnica de TPM se enfoca en analizar los posibles modos de falla de una máquina y sus efectos.
- Se trata de un análisis proactivo que busca prevenir posibles fallas y mejorar la fiabilidad de las máquinas. AMEF también ayuda a identificar los puntos débiles en el diseño y en el proceso de producción, lo que permite realizar mejoras y reducir el riesgo de fallas futuras.
Dificultades y desafíos del TPM
A pesar de sus múltiples beneficios, la implementación del TPM puede presentar algunos desafíos y dificultades. Algunas de las más comunes son:
- Cambio cultural: Para que el TPM tenga éxito, se requiere un cambio cultural dentro de la organización, que involucre a todos los niveles de la empresa. Esto puede ser difícil de lograr, ya que puede requerir cambios significativos en la forma en que se llevan a cabo las actividades diarias.
- Falta de compromiso de la gerencia: La implementación del TPM debe ser liderada por la alta dirección y contar con su apoyo incondicional. Si la gerencia no está comprometida con el proceso, es poco probable que tenga éxito.
- Falta de capacitación: Para que los trabajadores puedan participar activamente en la implementación del TPM, es necesario que se les brinde la capacitación necesaria. Si no se proporciona la capacitación adecuada, los trabajadores pueden sentirse abrumados o desmotivados.
- Resistencia al cambio: Algunos trabajadores pueden resistirse al cambio y a la implementación del TPM. Esto puede deberse a la falta de comprensión de los beneficios del TPM o al miedo a perder sus puestos de trabajo.
- Medición y análisis de resultados: La medición y el análisis de los resultados del TPM pueden ser difíciles de llevar a cabo. Es necesario contar con herramientas y técnicas adecuadas para medir y analizar los resultados, y asegurarse de que los datos sean precisos y confiables.
- Sostenibilidad a largo plazo: El TPM es un proceso continuo que requiere un compromiso a largo plazo. Es importante asegurarse de que se mantenga el impulso inicial y de que el proceso se mantenga a largo plazo para lograr los máximos beneficios.
Futuro del TPM
El futuro del TPM (Mantenimiento Productivo Total) es muy prometedor, ya que sigue siendo una herramienta esencial para mejorar la eficiencia y la productividad de las empresas.
Se espera que las empresas continúen adoptando el TPM como una forma de mejorar la calidad, reducir los costos y aumentar la satisfacción del cliente.
En el futuro, se espera que el TPM se integre cada vez más con otras tecnologías emergentes, como la inteligencia artificial, el análisis de datos y el Internet de las cosas (IoT).
Esto permitirá una mejor gestión de la maquinaria y la capacidad de predecir y prevenir fallas antes de que ocurran.
Además, se espera que el TPM evolucione hacia un enfoque más holístico que aborde no solo el mantenimiento de la maquinaria, sino también la gestión de la cadena de suministro, la planificación de la producción y la gestión de la calidad.
Esto permitirá una mayor integración y coordinación entre los diferentes departamentos de la empresa y, en última instancia, mejorará la eficiencia y la rentabilidad.
Resumen
El mantenimiento de producción total es un sistema programado de varios procesos que permitirán a las empresas sacar el mayor provecho a sus recursos. Este mantenimiento no solo consiste en mantener funcionando a los recursos por separado, pretende coordinarlos para que trabajen en conjunto y sobre todo incluir de forma significativa al personal.
El objetivo principal del mantenimiento de producción total es obtener un producto final de calidad, reducir costos, minimizar plazos, establecer procedimientos eficientes y crear un ambiente de unión entre el personal, los equipos y los procesos de producción de la compañía.
Las ventajas importantes de implementar el TPM están enramadas en tres sectores: la organización (mayor control, mejores procesos, ambiente laboral y prevención de contratiempos), la seguridad (mejores medidas de prevención, cuidado del equipo y salud del personal e identificación pronta de posibles fallas) y la productividad (cumplimiento de plazos, producto final de calidad, mejores condiciones de trabajo y mayor competitividad en el mercado).
Dentro de las posibles desventajas en el TPM podemos considerar: Una mala planificación si no toma en cuenta los fines y objetivos de la empresa, si no se implementa de manera escalonada según el momento en el que se encuentre la empresa o si se capacita al personal antes de darle mayores responsabilidades. Y no considerar imprevistos.
Para poner en marcha el mantenimiento productivo total se deben seguir estas cinco acciones: separar lo innecesario, situar lo necesario, suprimir la suciedad, señalar anomalías y seguir mejorando.
Siguiendo estas cinco acciones se pueden establecer los procesos del mantenimiento productivo total que son: Kobetsu Kaizen o mejoras enfocadas, Jushu Hozen o mantenimiento Autónomo, mantenimiento especializado, mantenimiento planificado o progresivo, Hinshitsu Hozen o mantenimiento de calidad, mantenimiento en la administración, capacitación y entrenamiento constante y seguridad y ambiente favorable:
Estos procesos trabajan en conjunto y es posible que no siempre estén implementados, esto ya dependerá de las características, principios, misión, visión, fines y desarrollo del negocio que se trate. Incluso depende del producto final que se desarrolle (bien o servicio).
Dime ¿Estás listo para incursionar en el mantenimiento productivo total?
🧐 Autoevaluación: Mantenimiento productivo total
¿Qué significa TPM en mantenimiento industrial?
¿Cuál es el objetivo principal del TPM?
¿Qué herramienta se utiliza en TPM para monitorear el estado de las máquinas?
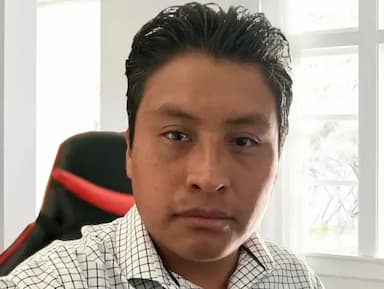
Juan Carlos García
Desarrollador de Software / Electrónica
Hola estudié Ingeniería Eléctrica - Electrónica en la UNAM y hoy en día doy mantenimiento a varios sitios web y plataformas de rastreo de activos móviles, y me he enfrentado a cada uno de los temas que propongo en Factor Mantenimiento, es por ello que comparto mi experiencia con el objetivo de hacerte a meno cada tema y no gastes tanto tiempo como lo hice yo, así que espero que este y todos mis post, te sean de gran ayuda.